Pyrolysis plastic to oil machine
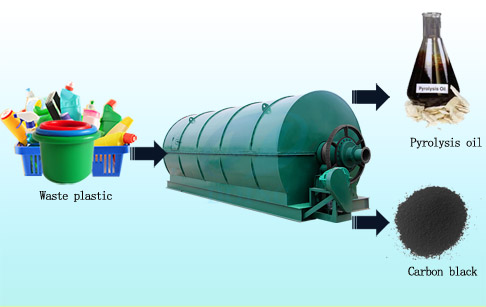
Pyrolysis plastic to oil machine
Plastic waste is the third largest contributor to municipal and industrial waste systems after food and paper. PE, PS and PP account for over 70% of this plastic waste produced all over he qorld.Therefore,significant amount of energy can be produced with this technology. This could be an alternative energy resource for substituting fossil fuels. The governments could reduce the reliance on the imported oils. The community may also reduce the reliance on the hydrolic power generation. The fuels produced from this process do not contain sulphur content because there is no sulphur in the waste plastic feedstock. This is an advantage compared with the classic fossil fuels because sulphur content in the fuels could form SO2 after combustion. SO2 is a pollutant causing severe air pollutions, which affects people health and damages the concrete structure.
Therefore,this technology is environmental friendly and has significant positive impact on the local government and community.
Pyrolysis is a thermal cracking reaction of the large molecular weight polymer carbon chains under an oxygen free environment and produces small molecular weight molecules.
Traditional treatments for post-consumed plastics were landfills or incineration. However, landfill of the post-consumed plastics has potential problems because of limited land resource and high durability of plastics.
Incomplete incineration may generate poisonous substances and causes serious health problems.
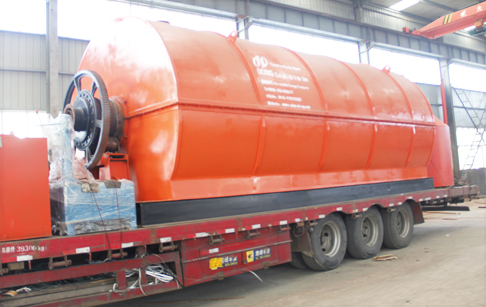
The selection of pyrolysis technology is based on the characteristics of the feedstock and the target products.In general,each pyrolysis technology consists of three parts:feeding system, pyrolysis reactor and separation system.
Pyrolysis plastic to oil machine Technologies and Processes:
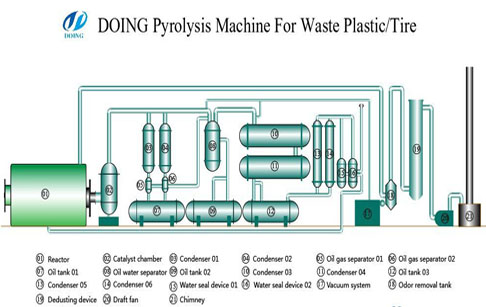
Pyrolysis plastic to oil machine working process
1. Put raw materials into reactor by auto-feeder, then heat the reactor with any one of the following fuel materials: coal, wood, natural gas, oil. Do not stop heating the reactor, when the temperature reaches nearly 250 degree Celsius, waste tyre will be transferred to oil gas.
2. The liquid oil will be cooled by condenser from oil gas and then collected by oil tank. Third, the exhaust gas which can not be cooled in normal pressure will be recycled to heat the reactor. In this way, you can not only saving energy, but also protecting environment.
3. Smoke produced by processing the tyres can achieve national emission standard through dual desulfurization and dusting removal device.
4. After you get oil, the temperature will be low, at this time, carbon black will be discharged automatically.
Last, when the temperature falls to 100 degree Celsius, worker could put steel wire hook to reactor to take steel wire out. After all these steps, you can start another batch.
Plastics like PE, PP, and PS can be considered as saturated alkene molecules due to their large molecular weight. PE is one of the most commonly used plastic materials.
Pyrolysis plastic to oil machine final product application
Fuel oil from used of Pyrolysis plastic to oil machine used in below industries
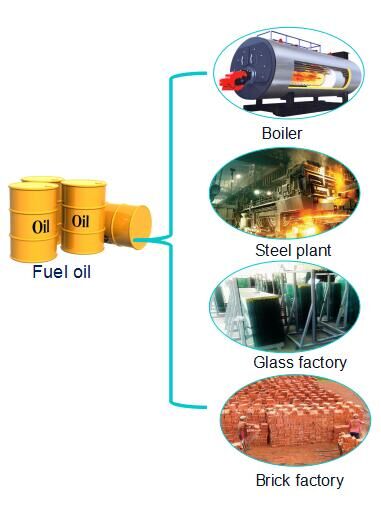
Fuel oil application
A.power plant factory
B.glass factory
C.cement factory
D.ceramic fatory
E.aluminum factory
F.boiler factory
G.central heating factory
H.painting factory
Carbon black from Pyrolysis plastic to oil machine
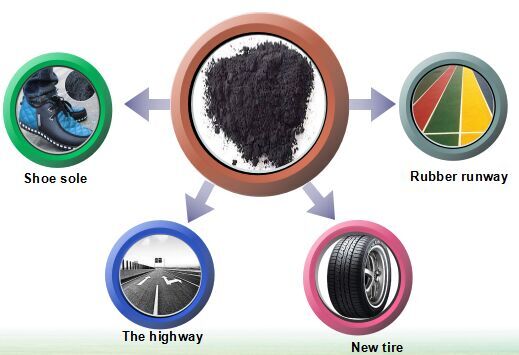
Carbon black application
B.Conveyor ban
C.Hose and doormat
D.Black nylon bag
E.Rubber additive
F.Automatic spare parts
G.Heat isolation
H.Black colorant in rubber materials