
What is the 2018 new design fully continuous waste plastic pyrolysis plant advantages?
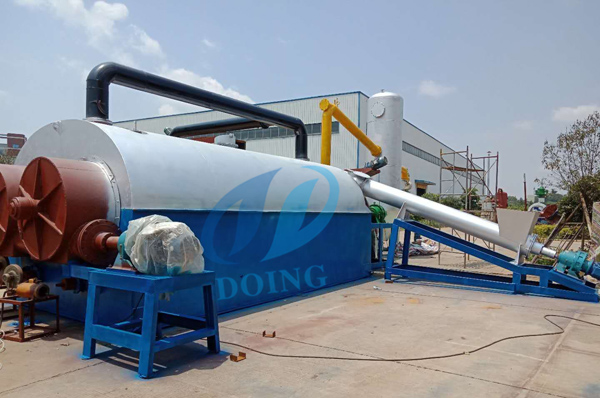
DoingGroup 2018 new design fully continuous plastic pyrolysis plant
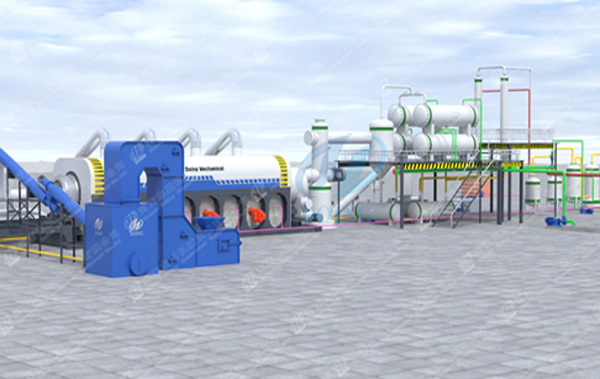
3D photo of DoingGroup continuous waste plastic pyrolysis plant
Item | Reference | |
1 | Working method | Fully automatic, no stop even a second. |
2 | Reactor Structure | The 6th generation, external reactor rotate. Material move inside reactor through a guiding device. |
3 | Reactor size | ¢1.2m ×9.5m according to real material |
4 | Reactor electricity consumption | 55 KW |
5 | Heating method | Indirect heating, no direct fire to reactor |
6 | Heating resource | Oil, recycled waste gas. |
7 | Cooling method | Recycling water (water consumption: 10 kg/t Evaporation loss ) |
8 | Sealing | Both hard and soft sealing. Mainly use soft sealing. |
9 | Control method | Intelligent, variable frequency automatic control +manual operation: also can be made full PLC system without any manual control according to customer requirement(price of this need to discuss) |
10 | Area | 1000m² |
11 | Application | |
12 | Reactor material | Q345R (stainless steel is available with different price if required) |
13 | Machine life | 5-10 years according to material |
The advantages of the 2018 new design fully continuous waste plastic pyrolysis plant :
1) Adapt to external rotation and uniformly heat the reactor 360°. No part of the reactor is heated for a long time, in this way, our reactor has a longer service life.
Internal heat transfer diagram of the reactor
2) Spiral blade design Inside the reactor, the raw material is run along the inner wall of the reactor. The raw material moves evenly inside the reactor, directly contacts the heat transfer surface, and immediately receives heat. The heat exchange is rapidly and evenly distributed, and the pyrolysis process is greatly improved.Schematic diagram of the dispersion of raw materials inside the reactor.
3) The reactor and feeder adopts frequency conversion explosion-proof motor, which can adjust the residence time of raw materials in the reactor according to the pyrolysis conditions of the raw materials in the reactor, so as to achieve the purpose of adjusting the processing amount and the pyrolysis state, so that the raw materials meet the requirements. In the case of a treatment amount, it is sufficiently decomposed to increase the oil yield.
4) Our reactor can be fed by steel wire free tire rubber particles and steel wire tire rubber particles. The carbon black can also be separated from the steel wire when the carbon black is discharged. If the raw material does not contain steel wire, the reactor can increase the processing capacity by 10%. In the process of discharging carbon black, the steel wire and carbon black can be cooled and can be directly collected and saved. Cooling time, improve production efficiency.
5) While using the burner as a heat source, our reactor recycles the non-condensable combustible gas generated by tire pyrolysis and passes the exhaust gas burner as the second heat source of the reactor to achieve "self-sufficiency" and save fuel consumption. Will reduce production costs and increase customer revenue. In addition, the flue gas after combustion of the exhaust gas is effectively treated to meet the environmental standards for flue gas emissions.
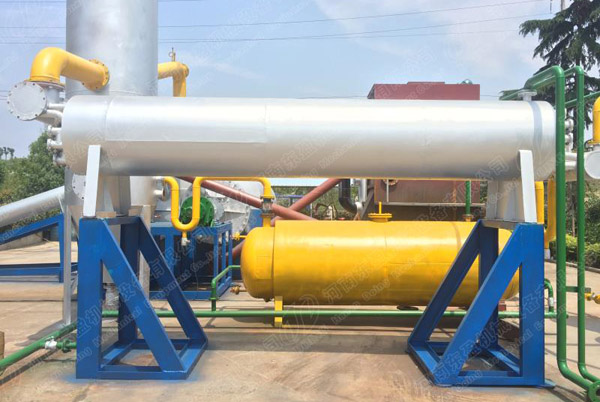
Continuous waste plastic pyrolysis plant